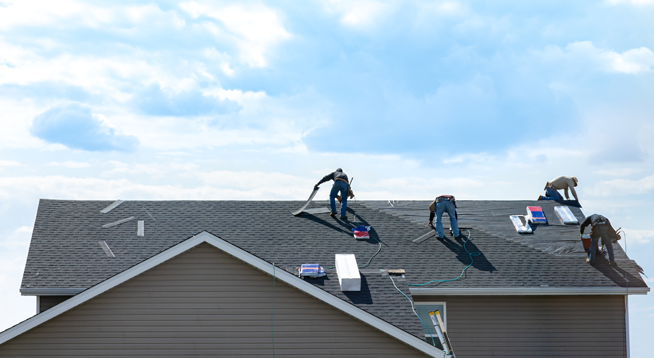
By Ken Calverley and Chuck Breidenstein
DETROIT, June 9, 2022 ~ You’ve heard us say it a hundred times during the 15 years we have been on air: A house must have a good roof and a good foundation. Like a father admonishing his child before letting her take the car out on a Friday night, the advice may grow wearisome.
But the longer we are around, the more we find that the implied need for system thinking as regards the roof is not assumed or even understood by most people.
Many homeowners, and even some industry practitioners, still view the roof as whatever shingle they are observing without an understanding of the other, very vital, components.
For example, we refer to the area where we see a lot of shingles on the roof as “the field.” Most people believe any issues they have with water intrusion from above will develop in the field, but the truth of it is that most active leaks will originate around either a roof penetration like a chimney, a plumbing vent pipe or a dormer, or at the intersection of two slopes, called a valley.
We also hear a lot of owners say something to the effect “Why all these issues now? We never heard all this system talk before. Must be yet another way to charge more money for the same product.”
The simple answer to that lament is that roofs are typically far more complex than they were 40 years ago.
Back then, the most complicated attic space we saw was the one around the upper space in a story and a half home, typically referred to as a “Cape Cod.”
This was built as an economical bonus space for growing families to finish at a later date. We didn’t care about energy efficiency, and we weren’t very concerned about comfort either. It was a space to throw up some knotty pine and a couple of bunk beds for the kids. Who cared if they were hot up there in the summer or required an extra comforter in January?
That design aside, most roofs were simple, low slope, gables and, like those new tires on your car that you only expected about 40,000 miles out of, we anticipated replacing the roof every 10 to 15 years.
Roofs have evolved to become a very pricey component of the home and are featured as a design element in the overall aesthetic.
The industry began building steeper sloped roofs with lots of intersecting offsets and dormers.
In a house that was typically as leaky with warm air as an open chimney, energy code requirements forced us to insulate the attic space as we would the rest of the building.
New and thicker product was developed by shingle manufacturer’s that visually highlighted the roof.
This new cost component created a demand by consumers for longer warranties that did not pro-rate themselves out of existence in 10 years. The reaction to this demand was to re-examine each piece of the roof, from drip edge to eaves flashing to pipe boots to substrate to roofing underlayment. The industry developed a system.
As an example, a good roofer decades ago would cover the entire roof beneath the shingles with 15-30 pound felt — what we call tar paper — to function as a stopgap if any water got under the shingles.
Today a good system will include a one-way-permeable synthetic underlayment that not only serves this purpose but can allow moisture beneath the roof deck to escape, thus extending the life of the deck and helping to minimize the opportunity for attic-trapped moisture to contribute to mold growth.
Ventilation of the attic space is no longer left to “code minimum” by professionals. Based on data provided by the retail installer, the manufacturer will provide specifications for air intake and exhaust product to be installed as part of the system to assure no heat or moisture buildup in the space.
A product commonly referred to as eaves flashing resembles a continuous synthetic rubber sheet and is installed at the lower edge of the roof to minimize potential damage from ice dams. Good companies may install several rows of this material to maximize protection.
A professional company will remove old shingle layers and decaying substrate and install flashing and counter-flashing materials around penetrations like those mentioned earlier.
All of this, properly done by factory certified companies, allows installing retailers to provide non-prorated, extended warranties, of 30-50 years, in many cases backed by the materials manufacturer.
So don’t even consider the roof as a DIY project or one that a group of friends will tackle on the weekend. Hire a company you can trust like those found at InsideOutsideGuys.com.
For housing advice and more, listen to the Inside Outside Guys every Saturday and Sunday on 760 WJR, from 10 a.m. to noon or contact us at InsideOutsideGuys.com.